DSE 5
I guess I dont' understand why these can't be cast from a high-tensile steel? Is it the same concern for quality control? Or an issue of cost?
mark 107
QuoteI guess I don't understand why these can't be cast from a high-tensile steel.
By "these" do you mean the cables, or do you mean the pins?
Mark
DSE 5
Sorry, I was replying to Rob's comment about the pins. Guess it could have been a more clear response.
Can the pins be cast? Or hot-forged vs welding?
The comment at PIA was that the welded pins cost around 3.00 to make vs the 1.00 that the current pins cost.
Can the pins be cast? Or hot-forged vs welding?
The comment at PIA was that the welded pins cost around 3.00 to make vs the 1.00 that the current pins cost.
Also new at PIA:
Aerodyne Research signed a licensing agreement with Bill Booth to install the Skyhook on the ICON
Aerodyne Research signed a licensing agreement with Bill Booth to install the Skyhook on the ICON
JerryBaumchen 1,457
Hi DSE,
For the most part, cast metal devices do not have the 'toughness' or durability/flexibility (many flexions) that forged or machined metals have.
Castings tend toward brittle breaks/fractures. They are dynamic failures and not gradual failures like forgings.
I didn't see it put heard that John Sherman gave a demo of his pins being bent back and forth numerous times through 180 degree arc before failure. Just to prove that they will stay together when flexed/bent.
That is one reason castings have never been used in this industry, military or sport.
HTH,
Jerry
For the most part, cast metal devices do not have the 'toughness' or durability/flexibility (many flexions) that forged or machined metals have.
Castings tend toward brittle breaks/fractures. They are dynamic failures and not gradual failures like forgings.
I didn't see it put heard that John Sherman gave a demo of his pins being bent back and forth numerous times through 180 degree arc before failure. Just to prove that they will stay together when flexed/bent.
That is one reason castings have never been used in this industry, military or sport.
HTH,
Jerry
DougH 270
QuoteAlso new at PIA:
Aerodyne Research signed a licensing agreement with Bill Booth to install the Skyhook on the ICON
That is awesome... let me know when I can send my rig in for retrofitting.
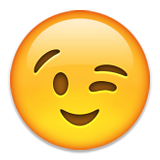
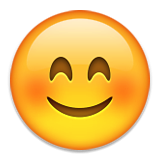
"The restraining order says you're only allowed to touch me in freefall"
=P
=P
riggerrob 643
Similarly, I heard that Sigmas are moving away from the stamped (from sheet stainless steel) reserve pins towards forged reserve pins. Sigma reserve pins are shaped similar to Sherman's welded pins, but thicker.
This is because forged pins will be stronger and less likely to bend. If they do bend, forged pins are less likely to crack. This is because the forging process aligns the grain of the metal with the exterior shape.
This the same reason PIA has not followed the custom automotive fashion of carving exotic parts for billet steel.
This is because forged pins will be stronger and less likely to bend. If they do bend, forged pins are less likely to crack. This is because the forging process aligns the grain of the metal with the exterior shape.
This the same reason PIA has not followed the custom automotive fashion of carving exotic parts for billet steel.
>>>>>>>>>>>>>>>>>>>>>>>>>>>>>>>>>>>>>>
It is a question f ripcord flexibility.
When pulled straight or at 90 degrees to the housing, Spectra ripcords have slightly less friction.
However, the big change occurs when you try to pull a metal ripcord at 180 degrees to the housing (i.e. towards your chin). Friction on metal ripcords get obscenely high, while Spctra ripcords are still pull-able.