The111 1
QuoteThis time for some reason it was a bit more difficult to get the plaster cast off the foam mold
Probably because the foam was filling the mold better and trying to adhere to the surface. Also, maybe you should have re-waxed the cast if you didn't.
Regardless, glad it worked out! I had a big divot in my foam head but I filled it in very carefull with microballoon putty. I used a trick where you put a few small nails in the divot area, sticking out too far, then use the cast the push all the nails in to the right depth so all the heads sticking out tell you exactly where the surface should be, if that makes any sense.
www.WingsuitPhotos.com
QuoteQuoteThis time for some reason it was a bit more difficult to get the plaster cast off the foam mold
Probably because the foam was filling the mold better and trying to adhere to the surface. Also, maybe you should have re-waxed the cast if you didn't.
Regardless, glad it worked out! I had a big divot in my foam head but I filled it in very carefull with microballoon putty. I used a trick where you put a few small nails in the divot area, sticking out too far, then use the cast the push all the nails in to the right depth so all the heads sticking out tell you exactly where the surface should be, if that makes any sense.
Yea it does that sounds like a good idea Matt. I did rewax the cast mold, I thought it would have been too tough to get it off If I didnt
Today I began the process of preparing the foam mold. Basically what this step is for is to prepare the mold for fiber glassing its pretty much a three step process, I'll describe each step as I do them. Yesterday, I woke up early for work and found the foam mold to be dry and cured so I decided to start step one of the prep before I went to work last night.
Basically what you do is take 100 grit sand paper and sand the surface of the mold. the trick is to scuff the mold up without sanding down too much of the foam. Sanding down too much of the foam will alter the final shape of the helmet. I had a couple of high points so I knocked them down a bit and I sanded the seam line down flush with contour of the head the sanding doesnt have to be perfect but if you do a good job its not as hard to get the resin to stick. So after I had the mold sanded, I mixed up a batch of resin, Wes's direction say to use the fiberglass resin, but after a conversation with him, he said he no longer uses the fiberglass resin he just uses the west system epoxy, he said it works just as well and doesnt have as much odor. So I mixed up the resin and added some coloring agent, Im using gray, and I sent of to work coating the foam mold. As I painted the mold, I thought damn it seems like I'm not getting anywhere. But the thing to remember is that the mold is pores and the pores have to fill in before you will get a nice even coat.. I used a three to three ration when mixing the resin and hardener Doing so gave me enough time to finish painting the mold before the resin hardened. I had to go back and get a little more mixture to do the whole thing but I got it done. When I came home today I found a couple of spots that still needed to be covered so I mix up a tiny bit more and finished them off. When the mold drys completely Ill move of to the next step in the prep process.
All and all this step was pretty easy, I do think I could have sanded down the mold a little more though.
Basically what you do is take 100 grit sand paper and sand the surface of the mold. the trick is to scuff the mold up without sanding down too much of the foam. Sanding down too much of the foam will alter the final shape of the helmet. I had a couple of high points so I knocked them down a bit and I sanded the seam line down flush with contour of the head the sanding doesnt have to be perfect but if you do a good job its not as hard to get the resin to stick. So after I had the mold sanded, I mixed up a batch of resin, Wes's direction say to use the fiberglass resin, but after a conversation with him, he said he no longer uses the fiberglass resin he just uses the west system epoxy, he said it works just as well and doesnt have as much odor. So I mixed up the resin and added some coloring agent, Im using gray, and I sent of to work coating the foam mold. As I painted the mold, I thought damn it seems like I'm not getting anywhere. But the thing to remember is that the mold is pores and the pores have to fill in before you will get a nice even coat.. I used a three to three ration when mixing the resin and hardener Doing so gave me enough time to finish painting the mold before the resin hardened. I had to go back and get a little more mixture to do the whole thing but I got it done. When I came home today I found a couple of spots that still needed to be covered so I mix up a tiny bit more and finished them off. When the mold drys completely Ill move of to the next step in the prep process.
All and all this step was pretty easy, I do think I could have sanded down the mold a little more though.
Why invest so much time in molding your own head when you've got such an easy way to do that. Find a company that makes 3D scans and cuts out the foam. A lot faster and cheaper I think.
All speeding past collide and crashing, I'm in paradise.
The111 1
QuoteA lot faster and cheaper I think.
Ok, what's the cost then? A head mold this way (the Wes way) should cost well under $100. The reason (I'm guessing) for Chuck's quoted cost so far is because he's already bought all his materials for the rest of the project.
www.WingsuitPhotos.com
QuoteQuoteA lot faster and cheaper I think.
Ok, what's the cost then? A head mold this way (the Wes way) should cost well under $100. The reason (I'm guessing) for Chuck's quoted cost so far is because he's already bought all his materials for the rest of the project.
Matts correct, the thing he's also not taking into account too is that when you buy resin, hardeners, foam etc your not just buying enough to make one helmet, there's probably enough left over when your done to make 3 more helmets so actually if you figure the unit cost its much less.
Today I continued to prepare the foam mold for fiber glass. I added sanded down the first coat of resin knocking off some high points and smoothing it out a bit and I added a second coat of resin. During this step the directions require that you mix the resin, hardener and then add the coloring agent after thats done you add some micro-balloons, I personally have no idea what the micro balloons are from a technical description (maybe Matt can provide more information) but from a basic stand point micro-balloons looks like red clay and they are used to thicken up the resin.
I mixed everything up and I added the second coat to the foam mold, Im not going to post any photos because it really doesn't look any different in the pictures. But sitting here in front of the mold I can tell you about it, the resin with the micro balloons has started to fill in alot of the rough and low spots the mold looks much smoother. and its starting to take shape..
The next step will probably be the longest in preparing the helmet for glass, basically I have to mix the resin, micro balloons, hardener, and coloring agent to the thickness of body filler using that compound I have to fill in all the divots and defects until the entire mold is smooth. I expect this step to take at least a couple of layers, as it is not something that can me done half assed. I'm going to let this coat of resin harden over night and I'll probably start the next step tomorrow, I would venture to guess as far as work hours Im probably into this project 5 hours of actual labor time, the longest part of this project so far has been the wait time, after every step you have to wait at least 12 to 24 hours for drying time.
What I learned today
It takes a fairly good amount of micro balloons to thicken the resin up, but you have to add alittle at a time or you'll add to much and end up wasting the mixture if it becomes too thick.
When you are using the micro balloons you have to use more of the coloring agent, the balloons are red in color and they absorbed some of the gray tone from the coloring agent. Not a problem just an interesting fact.
Some of what I am writing may not make sense until you have your directions in hand hell even then some of it might not make sense.
Until tomorrow.
Chuck
I mixed everything up and I added the second coat to the foam mold, Im not going to post any photos because it really doesn't look any different in the pictures. But sitting here in front of the mold I can tell you about it, the resin with the micro balloons has started to fill in alot of the rough and low spots the mold looks much smoother. and its starting to take shape..
The next step will probably be the longest in preparing the helmet for glass, basically I have to mix the resin, micro balloons, hardener, and coloring agent to the thickness of body filler using that compound I have to fill in all the divots and defects until the entire mold is smooth. I expect this step to take at least a couple of layers, as it is not something that can me done half assed. I'm going to let this coat of resin harden over night and I'll probably start the next step tomorrow, I would venture to guess as far as work hours Im probably into this project 5 hours of actual labor time, the longest part of this project so far has been the wait time, after every step you have to wait at least 12 to 24 hours for drying time.
What I learned today
It takes a fairly good amount of micro balloons to thicken the resin up, but you have to add alittle at a time or you'll add to much and end up wasting the mixture if it becomes too thick.
When you are using the micro balloons you have to use more of the coloring agent, the balloons are red in color and they absorbed some of the gray tone from the coloring agent. Not a problem just an interesting fact.
Some of what I am writing may not make sense until you have your directions in hand hell even then some of it might not make sense.
Until tomorrow.
Chuck
DSE 5
A 3d head scan and milled print costs around 125.00.
Detail can be cleaned up prior to the print/milling. Milling can be done on foam, a paper-like product whose name escapes me, wax, and a few other plastic products.
Hair must be netted down or contained, because the scanner will see every hair as a detail point that can seriously eat up CPU time.
One benefit is speed. Make a scan, have the head/mold done in about 30 minutes or less, and it'll be a perfect likeness, including eyes, nose, mouth...basically it's a perfect copy of your face/head.
There are printers all over the world, or you can email an .stl file to someone to print for you.
Detail can be cleaned up prior to the print/milling. Milling can be done on foam, a paper-like product whose name escapes me, wax, and a few other plastic products.
Hair must be netted down or contained, because the scanner will see every hair as a detail point that can seriously eat up CPU time.
One benefit is speed. Make a scan, have the head/mold done in about 30 minutes or less, and it'll be a perfect likeness, including eyes, nose, mouth...basically it's a perfect copy of your face/head.
There are printers all over the world, or you can email an .stl file to someone to print for you.
mccordia 74
QuoteA 3d head scan and milled print costs around 125.00.
Or do it the 'cheep' way, and use a 3D matchmoving program to generate a 'scan' from your head, by shooting several passes of your head with a videocamera.
Then take the resulting point-clouds, and convert those to a 3D mesh, and find the overlaps and 'you have a 100% accurate resprentation of your head. (Drawing dots or adding tiny markers to your face helps in the accuracy)
THEN print 40 or so cross-sections, and paste thos onto 1 cm thick wood.
Then sand down the transition from each piece to another, and 'voila'. With only 5 weeks of fulltime work, you have a wooden head
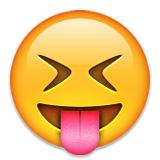
ps. Though possible, and the first step (cheep 3D scan) can be done in a day or so. Its a joke..and definately not something Id wish for ANYONE to actually do
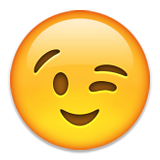
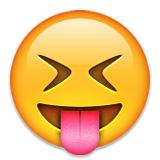
JC
FlyLikeBrick
I'm an Athlete?
FlyLikeBrick
I'm an Athlete?
sounds cool but where would you get it done??
even after you have the foam mold done, you would still have to prep it with resin to prepare it for fiberglass. the foam mold cost me 20.00 for four rolls of plaster and about 20.00 for expanding foam and probably 1.5 hours worth of labor. Although it would be nice to know that the mold is a perfect replica of your head, takes alot of the guess work out later wondering if you did everything right.....
even after you have the foam mold done, you would still have to prep it with resin to prepare it for fiberglass. the foam mold cost me 20.00 for four rolls of plaster and about 20.00 for expanding foam and probably 1.5 hours worth of labor. Although it would be nice to know that the mold is a perfect replica of your head, takes alot of the guess work out later wondering if you did everything right.....
DSE 5
There is a place in Provo, Utah that does a variety of 3D scan products. One of them is that for 195.00, they scan your head, mill the bust, and coat it with a brass/bronze-like substance that is fairly hard. When they give it to you 3 days later, it looks like a bronze bust, but weighs basically nothing.
If you have to prep the head with resin for fiberglass/CF, it seems like there isn't any cost savings, and only a couple days of time saved by having a head milled. And, I'm not certain that many of the foams or wax they use for the bust/print would be amenable to being covered in resin?
If you have to prep the head with resin for fiberglass/CF, it seems like there isn't any cost savings, and only a couple days of time saved by having a head milled. And, I'm not certain that many of the foams or wax they use for the bust/print would be amenable to being covered in resin?
johnboy 0
Would there be any benefit to doing this with carbon fiber vs fiberglass? Seems to me there might be some weight savings, even if not much, but I can defenitely see the cost going up a bit too.
I'm assuming the comfort level goes up a bit with a custom lid as such. Not to be confused with a camera helmet being comfortable. But I do like how much more comfortable my Hanson is vs my FTP. I see helmet building instructions in my near future.
I'm assuming the comfort level goes up a bit with a custom lid as such. Not to be confused with a camera helmet being comfortable. But I do like how much more comfortable my Hanson is vs my FTP. I see helmet building instructions in my near future.
There is not much difference between carbon fiber and fiber class. Except, carbon fiber is MUCH more expensive and is a pain in the ass to work with when you are sanding etc. You certainly can build a CCM using carbon fiber, but I just don't see and advantage to it as opposed to fiber class. I will be using carbon fiber for the top plate, I found (thanks DSE) a source that sells solid carbon fiber plates by the foot. Sure beats the hell out of making my own and cost about the same.
The111 1
QuoteWould there be any benefit to doing this with carbon fiber vs fiberglass?
The major difference between carbon fiber and fiberglass is stiffness (and strength, to some extent). Fiberglass is strong enough, however, and for the helmet shell stiff is actually not what you want. For the top plates, you do want stiff.
www.WingsuitPhotos.com
fr33flyr 0
Where can I buy a copy of the cd insructions? I went to Wes' website but I didn't see any ordering info.
_______________________________
I like life....It's something to do.
_______________________________
I like life....It's something to do.
The111 1
tso-d.com, call them if it's not on the site.
www.WingsuitPhotos.com
I took two seperate cups, I poured 6.25 ozs of each of the two parts of the expanding foam mix in each of the cups I then poured the contents of the two cups into one and stirred the mixture for about 35 to 40 seconds to make sure it mixed together well, I stirred it kinda briskly but was careful not to make bubbles. I then slowly poured the mixture into the plaster cast tipping in forward a bit to make sure the chin area was full. Three hours later I seperated the plaster cast from the foam mold. This time for some reason it was a bit more difficult to get the plaster cast off the foam mold but the results were remarkably better! The foam mold is smooth, the area where I had the mask opening is well defined and the contour of the chin is easier to work with. I would not have been able to fill in the contour with resin and I would not have a helmet that fit later.
Lessons I've learned today,
1) Take your time, it took me 15 minutes of work and three hours of wait time to ensure this step was right. If I had proceeded with this project without redoing this mold my helmet would not have fit right and I would have had wasted HOURS of work and had to return to this point and start over
2) read the damn directions two or three times before beginning a step. I was looking back over the directions from when I made the plaster cast, when I put the scuba hood on I pulled the bottom of the opening over my lips Im not sure why I did that but I thought I was supposed to. the lower edge of the opening of the scuba mask should have been below my lower lip It's not a big deal and Im sure I can fix it later when I go to cut the opening for the the face, but its going to make more work for me later.
So thats where I'm at now, I have to let the new foam mold cure for at least a day. I have to work Tuesday night so Im going to leave it to cure until Wednesday morning then I'll go from there. I'm going to continue to to post my lessons learned and mistakes I make so that other people will not make the same mistakes even if it make me feel like a dumb ass. Hey
I'll be the first to admit I have no clue what the hell I'm doing but I'm learning as I go
New photos attached
Share this post
Link to post
Share on other sites