Recommended Posts
Not that it's skydiving related, but this just shows how stupid apathy/complacency is....
A recent tax bill just got defeated here. It would add $11 a year to your total property taxes. The money was to go to construction and staffing for a new Fire Station. All the studies that have been done show that the town REALLY needs another one, but with all the new taxes and fees Californians are being stuck with, $11 more was just too much.
Nearly 70% of the population couldn't see spending another $11 to reduce fire response times by almost half. They're complacent, because they don't need the services every day...
Skydivers were complacent about ripcords...until they got scared. So the question is, will we become complacent again, or will be foot the extra bill to make our gear better....? No one has died because of this scare. No one has lost a friend or loved one because of this. We weren't bitten, just scared...and you can quickly recover from being scared...
...My guess is we'll fall back into being complacent once this is sorted out. Money will be tight, and jump tickets are a more attractive place to spend your $$.
Just my $.02, for what it's worth.
"...and once you had tasted flight, you will walk the earth with your eyes turned skyward.
For there you have been, and there you long to return..."
sundevil777 102
QuoteAs much as people bitch about gear costs, do you really think they'll be willing to pay even more for a super reinforced pin??
I think you've got it! Maybe if manufacturers only sold the stronger pin when used with some sort of new, hot looking-sexier handle, then it would be popular.
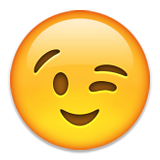
Maybe it is all in the marketing.
I think taxpayers turning down new levies is a response to the perceived waste & fraud in government.
councilman24 37
The pins are made by a cold forging process and must be able to be swaged to the cable. It's a trade off between strength (or stiffness) and malability to enable manufacture and swaging. Too hard and you can't attach them to the cable.
Of course the mil spec was for pins used with cones. The sport industry, and the military in borrowing from the sport side, are now using them for something completely different. I agree there should be a better pin for sport applications but the time and sales needed to recover the engineering costs and tooling are probably prohibative. Main pins, and RWS RSL reserve pins, which are not swaged could be and were readily adapatable to stronger materials.
Terry Urban
D-8631
FAA DPRE
sundevil777 102
QuoteThe pins are made by a cold forging process and must be able to be swaged to the cable. It's a trade off between strength (or stiffness) and malability to enable manufacture and swaging. Too hard and you can't attach them to the cable.
There are other ways of making a pin stronger. It could be a larger diameter. A stronger pin made of a different material could be attached to the cable with a separate, malleable swage. The RWS reserve pin is separate from the cable and attached without the normal swage. There are others.
billbooth 10
QuoteBack in the late 1970s - early 1980s, Hank Asquito built a bunch of straight ripcord pins. Since they were just swaged onto the end of the cable - with no shoulders - it was possible to insert them too deep into the loop, making for an obscenely hard pull.
I never heard of this happening in practice, but it always worried me when I packed Streamlite containers.
They were not swaged onto the cable. It was a stainless steel cab that was silver soldered onto the end of the cable. You never heard of it happening because it never did. If you followed the packing instructions there was no need to worry. As with other things on a sport rig, when used properly they work fine.
Sparky
QuoteThat's why we test 100% on ripcords...300 lbs. for 3 seconds
Just out of interest, what proportion of the ripcords you make fail the test and get binned.
Is this a common tests for manufacturers to do, or is my next rig going to be a vector
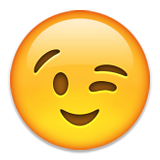
riggerrob 643
QuoteQuoteThat's why we test 100% on ripcords...300 lbs. for 3 seconds
Just out of interest, what proportion of the ripcords you make fail the test and get binned.
Is this a common tests for manufacturers to do, or is my next rig going to be a vector
>>>>>>>>>>>>>>>>>>>>>>>>>>>>>>>>>>>
Ripcord testing procedures vary widely from one manufacturer to the next. Most harness/container manufacturers just trust that ripcord manufacturers do their job properly.
When I built ripcords at Butler Parachute Systems, I did lots and lots of pull tests.
For example, when I worked at Rigging Innovations, we pull tested tested 10% of every batch of ripcords that came in the door.
On the other hand, when I worked at Para-Phernalia, most of the ripcords were manufactured somewhere else and they were lucky if they got a quick visual inspection.
QuoteQuoteThat's why we test 100% on ripcords...300 lbs. for 3 seconds
Just out of interest, what proportion of the ripcords you make fail the test and get binned.
Is this a common tests for manufacturers to do, or is my next rig going to be a vector
TSO-C23d (AS8015B) require that every reserve activation devise (ripcord) be tested to this standard.
Sparky
billbooth 10
By the way, TSO standards require that your ripcord DESIGN pass the 300 lb./3 second test, but does not state that you have to test every ripcord. You could choose to, for instance, test only 10%. However, since even one bad ripcord can ruin your day, we do 100% testing. We have added the new 11 lb.,4x90 degree side load test on every ripcord, simply because I no longer trust currently manufactured ripcord pins. The amount of incoming material testing I have to do now is at least three times what is was in the past, because of the generally lower quality of received goods. We now even have to test every friction adapter for slippage. One batch will come in that doesn't slip until 1,200 lbs., yet the next batch, from the same company, might slip at 300. Kevar went to crap about 4 years ago, and I had to redesign the lower bridle on my drogues to be easily replaceable, because now the drogue envelope now outlasts the drogue bridle...exactly the opposite of a few years ago. And don't even mention Velcro...It is nowhere near as good as it once was. I could go on and on...but that's my problem, not yours. What you get, in the finished product, at least from us, is the best materials available.
QuoteTSO standards require that your ripcord DESIGN pass the 300 lb./3 second test
Is this typical of the TSO standard. IE how much of the testing done for the TSO is pure design testing as opposed to testing the materials and the finished product
QuoteThe amount of incoming material testing I have to do now is at least three times what is was in the past, because of the generally lower quality of received goods.
This is starting to worry me a bit. If the quality of materials fluctuates (pins, webbing, etc) and there are sections of the TSO standard that only apply to the design, how many rigs out there wouldn't pass the TSO because the quality of the materials has changed since the initial certification???? Very scary
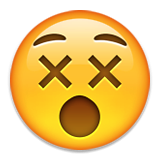
Think my next rig will be a vector
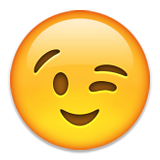
I'm one, with precise measurements, manufactoring tolerances and a definition of the used alloy the needed force to break a pin, and where it will break, is not that hard to produce.
In the case of simulating various kinds of stress on the pin to break it (leaning against and/or bumping into and/or....) we are talking about a whole different ballgame. I would not really know where to start that one.
#8
Share this post
Link to post
Share on other sites