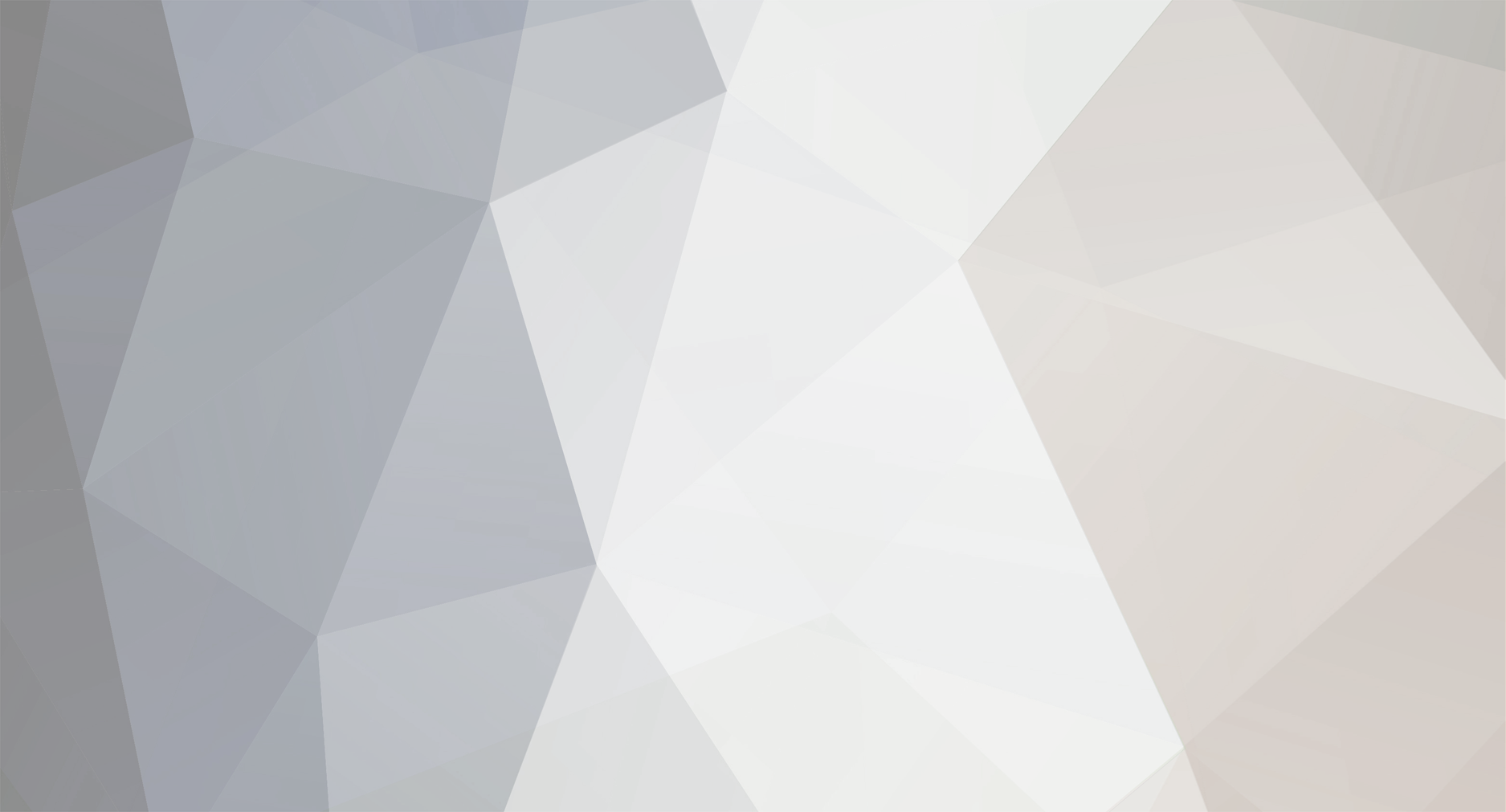
df8m1
Members-
Content
346 -
Joined
-
Last visited
-
Feedback
0%
Content Type
Profiles
Forums
Calendar
Dropzones
Gear
Articles
Fatalities
Stolen
Indoor
Help
Downloads
Gallery
Blogs
Store
Videos
Classifieds
Everything posted by df8m1
-
It would be nice if it was like that. Although I am getting way out my comfort zone (as in I could be talking out my XXX), I think this is getting into the area where Reynolds numbers come in to play, and I think Lee might be better suited to answer your question. The shape of the jumper has a lot if influence in regards to air flow. At very low speeds the flow of air around the jumper is pretty laminar and there is not a significant pressure differential. The air flowing around the jumper is adhered to the boundary layer so to speak. Like your tires will start to give way in a high speed turn, so will the air start to brake away from the boundary layer as speed increases, and turbulent flow starts to be created, as well as a pressure differential due to the inability of the air to stay adhered to the boundary layer. I would think that the pressure differential increases in steps as apposed to a curve as you have suggested. I imagine that at low speeds the air is relatively smooth, and as the speed increases, the air behind the jumper starts to become very unstable as the air starts to tare away from the boundary layer at the center of the back of the jumper. At the beginning stages of the tare away, I would expect to see the pressure differential to be "pulsey" or intermittent and erratic. As the speed increases the last tendency for the air to try to cling to the boundary layer is over come and a calmer pocket is generated at the surface of the boundary layer in the center, (right on the back of the jumper where the AAD is). Beyond the point where the air can no longer can hold on to the boundary layer, I am not sure how the pressure is affected at a given point on the boundary layer, as speed is increased. The turbulent burble behind the jumper changes shape, and I would think that the pressure would also continue to drop, although the exact ratio to speed I have no idea. The pressure differential at boundary layer of a belly to earth jumper seems to be in the 150 to 250 ish range at terminal, but a the width of the jumper has a lot to do with that as it is easer for air to flow around a skinnier jumper with a tight nylon suit, as apposed to a wide jumper with a baggy cotton suit, even taking into consideration that the wider jumper usually as a more rounded frontal profile which helps the air flow around the front of the jumper, “splitting” the air making a wider burble. That is what makes flying tight with a tandem challenging, as you get sucked into the burble and become part of the new frontal profile, the same affect can be felt as you pass a semi truck on the high way. This is one of the theories as to why the two jumpers that went in. If they were side by side, as in the instructor docked on the student, then the combined frontal area would change the shape that the air has to flow around, and there for affect the pressure at the back of the jumper where the AAD is. Formations slow down as more jumpers dock, this is because, 1, jumpers tend to relax and dearch once they are holding on, and 2, the growing frontal area that the air has to flow around is increasing. Now does this mean if you had a 3way compressed accordion that the center AAD would think it is higher than the 2 outer AADs? That is one of the tests we will be doing this summer to find out. Generally speaking, it is not a good idea to be close enough to another jumper at 1000 ft to affect each jumpers burble. Based on that, I compensate the activation altitude as speed increases beyond X, not so much because the pressure drops, but to compensate for the velocity of the jumper and the additional distance the jumper will travel during bag extraction, with the goal being to have an open canopy by a given “consistent” altitude, as apposed to looking at it as a firing altitude. Altitude variations from body position (belly to earth, or back to earth) are corrected based on pressure and orientation data. That not an exact correction, but the goal there is to reduce the actual altitude variation to less than 70ft, as apposed the 200ft or 250ft. This would translate in to a canopy opening altitude range of 1000ft to 930ft as apposed to from 1000ft to 750ft firing altitude range that results in an open canopy much lower. Now people will say that if the AAD is set to have an open canopy at 1000ft and the jumper is falling like a brick, then if they pitch at, say 1700, then the correction for the high speed would most likely result in a 2 out scenario, and they would be correct, and that is why the AAD must also realize that the jumper has deployed the main and to all delay firing in order to allow the main a chance to open above a hard deck altitude where if the velocity of the jumper is still above X, then the AAD will then deploy the reserve, as a last ditch effort to save the jumper. Even if the pressure differential is affected by two jumpers close together, that still does not explain why the other solo AAD fire with impact at line stretch might have occurred. I think I recall hearing in one of the videos that there have been 13 cases where a jumper has impacted at reserve line stretch after an AAD fire? Do the AAD companies still count them as a save? Not to imply that the AAD was at fault, but no one can really say at this point if it was or wasn't.
-
Thanks, I figured that they would continue to record, but I was not sure. Here is a question for any lawyers out there... Given that a jumper purchased the AAD, that recorded data during a jump that might be in question. Who owns the rights to that data? Is it the jumper's data? as it was recorded on a device that he/she purchased, during a jump that he/she paid for? Or does the manufacturer have sole rights to the data? and there for has the right to decide if it is released or "shared"?
-
I saw this link in another Reserve thread and I thought it related well to this discussion. While watching it, I saw another presentation of AADs from a different presenter but at the same event. It is a seminar from a BPA Expo, I assume their version of the Symposium we have in the USA. Gear Compatibility (Mark Procos) https://www.youtube.com/watch?v=1khn7DY9OPk&feature=player_detailpage&list=PLMqCekDhfSja0GAZnz34dY2cyYZQNQFEb#t=1249 AADs (Tom Noonan) https://www.youtube.com/watch?v=OOMSaIM92Hg&list=PLMqCekDhfSja0GAZnz34dY2cyYZQNQFEb&index=12 The first thing that I noticed is that the testing that was discussed was very similar to a proposal I sent to UPT and Strong Enterprises several years ago, and was told that there was no interest in that kind of testing. How times change lol.. I would be very interesting to know if the load cell data is synchronized or just individually recorded and then lined up as best as they can. Perhaps this is what John Sherman was taking about regarding the Deland Project? I definitely get the impression that the idea of an AAD firing at a given altitude is out the door so to speak and the idea that the AAD may not be compatible with certain reserves, body positions, or speeds… One point that I have not heard publicly discussed before is that the AAD operates on a “virtual” altitude and not the actual altitude that the jumper is at. Also that there is a wide window in which the AADs on the market “can/could” fire at, and that different AAD firing methods have an effect on how fast it can fire once the decision has been made to do so, yes some of this information has been in the manuals, but marketing companies like to talk about reliability, not the tolerances that could be easily exceeded which could result in the AAD firing deeper than advertised. It is good to see that the information is being presented. I heard a couple of times that it is impossible to know when the AAD fired from it’s data record, because it’s altitude is based off of where it thinks it is, or a virtual altitude created by the presence, or lack of a burble. That I disagree with, and unless the AAD stops recording data when it fires, the information is there to calculate a reasonable altitude “window” where it actually fired. It was stated that if the jumper was belly to earth at the time of firing, then the recorded altitude would be higher than the actual jumper AGL, because of the burble created by the belly to earth body position, and as such the actual firing altitude could not be determined. If the AAD stopped recording at the point in time when it fired, then determining what the actual AGL firing altitude was would be extremely difficult to determine if not impossible, as the only data that there is to work with, says the AAD performed as designed. However, if the AAD continues to record data until “after” it has landed, then there is enough data, even at 8sps, to arrive at a reasonable altitude range that it actually fired at. Lets look at a worse case scenario, the jumper is rock solid stable in a belly to earth body position, and falling like a rock at 190MPH. The AAD will be in a burble and most likely traveling faster than its “ideal” velocity, meaning that at the higher volicity the time it takes the AAD to be ready to fire “may” put the jumper closer to the ground than advertised. Working with that situation, the high speed jumper with the AAD in a burble, the AAD determines that the jumper is at the firing altitude and is exceeding the firing descent rate so it does what ever it does, thinking it is where it thinks it is, and the reserve pack is opened. At this point all the data that has been recorded would indicate a jumper falling at a high fall rate, but that the AAD fired at the proper altitude, which would explain why every time after an incident, the AAD’s data indicates that it fired at its proper altitude. If the AAD continued to record data, at the same sample rate, for a period of time after landing, then the data would allow the jumpers velocity to be calculated, and the time from when the AAD fired to when the jumper was pulled from the belly to earth body position to an upright position by the drag of the reserve deploying, which with only a baro sensor, would be indicated by a sudden decrease in altitude as the AAD is now not in a burble. We also have the time till landing as a reference number to work with if we wanted to. If we were to look at from the time where the AAD fired, to where the jumper became up-right in the saddle (for lack of a better description), indicated by a sudden decrease in altitude that is “stabilized” as not to be confused with a tumbling jumper, then we have the time it took from firing to the saddle. We could calculate the jumpers velocity at the time of firing, and calculate the distance the jumper traveled during the time from the firing to the saddle. In the upright or saddle position the AAD is not in a burble as it is in a belly to earth body position, and the altitude reading should be very close to actual AGL altitude if the AAD was properly calibrated to the local barometric pressure at take off. With the distance that jumper fell from firing to the saddle “estimated”, and then added to the earliest saddle indicated altitude, then an the actual AAD firing AGL altitude could be “estimated” providing for a reasonable range given the limited data to work with. If there was accelerometer data, then that could be used to help tighten up the estimation, but it sounds like there is only baro data being recorded by the Vigil and Cypres, not sure about the M2. Measuring the extraction forces is a good step. “When you have eliminated the impossible, whatever remains, however improbable, must be the truth”. There are several separate systems that have to work together during an AAD fire, and each system has its range of operation by design. I have decided to design and build a vertical drop test dummy that will allow the performance limitations of every aspect of the gear system to be determined, in as controlled and consistent conditions as possible given the technology presently available. Actual AAD activation altitude, as it is affected by speed, can be determined in a controlled vacuum chamber (as long as only Barometric pressure is measured to determine firing conditions), as well as in the air. On the other hand, Reserve Canopy opening distances, Pilot Chute pull forces, and Free Bag extraction times, can only be measured in the air, under known, controlled and consistent conditions, with the data to reference the test conditions to. I am very interested to see how the tests were conducted and how the data was collected and analyzed. I am even more interested in how the “industry” reacts to the data if it does show that there is a wide range of performance between the different manufacturers.
-
We are on the same page I think. Knowing what our gear will really do is the target. The parachute industry is so far behind in testing technology compared to the Automotive industry. I get lots of interest in data collection systems but only the USDA Forest Service has been interested in spending the money to start implementing even simplistic data collection to their parachute development programs. There are a lot of assumptions that data disproves, and it is funny to watch people new to the data collection and analysis come to that realization. It is not uncommon to get a call saying that there is something wrong with the data recorder because it is indicating X is going on and everyone thinks that is not happening. I take a breath and ask them to look at the other instruments and see what they are saying. Hardly ever does only one instrument pick up something that others do not to some degree, which is very helpful when trying to determine if a random spike is noise on a channel or something that happened during the flight. Then the light bulb goes on and they are like a kid that knows a secret that no one else does lol… And one of the aspects of the testing I am proposing is to allow everyone who is interested, to learn the secrets of the gear that they are using, or are considering buying. Would this information influence their gear choice? Perhaps, but keep in mind that the majority of the market is hooked on the cool aid to reference an accurate comment I received recently. I am kind of surprised that we have not heard from the usual advocates of testing and gear performance standards. Perhaps I am way out there in la la land, and destined to be strapped in a straight jacket for my own protection and they don’t want to he associated with the notion . lol It will be interesting to start testing the different conditions that were associated with the incidents where an AAD fired and the jumper impacted at line stretch. The situation where the jumper pulled the handle and captured his reserve pilot chute in tow is straight forward to me, the pilot chute could not pull the free bag out due to a bad combination of design and components, and I think that the general combination is known. I also think that an old student rig doesn’t fall into that combination category, but I could be wrong. Does anyone know if the foreign jumpers brought their own gear, or if they rented it from the DZ? My partner brought up the possibility of different reserve repack and maintaince standards around the world being another possible domino.
-
So do I put you in the nay category then? lol... But seriously... You bring up some good points, some of which my partner brought up last night as well. As I have said before, pier review is very important in the idea development process. You are correct about my intentions about a “Rational”, or as I think of it, a “common sense” standard, which in reality, all the existing standards intend to do in spirit, but seem to have politics imbedded in them to allow for interpretation, and at 750ft interpretation is not going to save our butts. I get the feeling that you are concerned that if the existing gear is tested vertically at 150 Knots, with the 245lbs weight (or what ever the speck is), and activated at 1000 ft AGL that a there will be a large percentage of impacts? And that, if that were to happen, and the validity of the tests were solid, then that would have a negative reaction of a cataclysmic nature? Keeping in mind that any theoretical gear that failed would have passed the TSO standard set by the Feds, so where does the pressure lie? I’m not sure… An argument to not develop a vertical test platform that will allow for real world testing (validation) for fear that it “could” possibly identify some equipment that would not save a jumper from 750 or 1000 ft, and therefore would negatively affect the “sport” is not a good one in my opinion, (I don’t think that is what you were trying to say, but I have gotten that argument from others). Or that the manufactures would through up their hands in the air and say they are going to have to double the cost of the equipment in order to not build gear that might not save you.. Or, I’m sorry, but this year 5 of our fellow jumpers will have to be sacrificed so that we can afford to buy our gear and continue to have fun… This concludes my Counter Rant… LOL I really am not thinking of a “new standard” at all, just a process to “Validate” that the TSO standards truly are in our best interests at 750 ft. We as jumpers have been given the freedom to self regulate, is this concept not within the sprit of that idea? If there is the impression that I am wringing my hands with dollar signs in my eyes from how much money could be generated by creating gear fear, then I have failed to convey my feeling of genuine responsibility to try to answer questions as to why two jumpers both died at the same time, or why any of the other jumpers went in because their reserve did not open in time after their AAD fired, given that I have a foundation for the technology necessary to create as realistic of a test environment as possible,(in theory), and without risking a jumpers life to do it. Yes there will be costs associated with the testing, I have rented a Skyvan to do drop tests in the past and have made craters in Area 51, and if we wanted to have a drop test boogie then we could cover the cost of the plane and have fun at the same time. The test “platforms” as I call it, need to be cheap to build as they need to be consumable, but protect the instrumentation so it can be reused saving costs. There is a reserve that some have very publicly questioned its vertical opening distance speck, either due to the horizontal manner in which it was tested, or from incidents, I do not know. (I do not want to bring names into this because that is not the point) Now, if this reserve was to be tested in a strictly vertical path, at the TSO speed and weight for that canopy, and after 10 drops, of which the data from each platform was compared to insure the tests were truly consistent and comparable, and the results showed that the reserve does indeed operate with in the TSO 300 Vertical ft, or 3 sec rule, I think that would be important to know, as we would then need to look at other possible causes for the hypothetical slow opening problem, which could also be validated or disproven to exist it self. You may have identified the reason that PIA has not made any progress on this issue, or at least if they have, they have not published any information on it. John Sherman mentioned something about a Deland project a few posts back, but I have no idea if that is DRC or Parachute Labs, or PIA… It is not my intention to cause panic, fear, stir the pot, or make an absurd amount of money from this processes, ( but a little for the investment would not hurt :) ) I still have my first rig that I bought brand new and is has about 800 jumps on it, or on the main I should say, as the reserve has never been used, not once even tried…. Anyone ever bought a brand new car that has not had the engine started yet? Wouldn’t it be funny to go out the dealer lot, get in your new car, turn the key and nothing happens… 750 or even 1000 ft is a bad time to find out that your reserve won’t start in my opinion. Right now that is our only choice. It is unfortunate that the majority of jumpers, and I think more so of the new jumpers, are more concerned about looking good as the EMS guys are cutting the harness off, then how and why their gear works so they can make an informed decision as to which gear to use for what they want to do. If I am a head down jumper then the idea of a slower opening reserve might sound appealing, and I would then need to know how far it will take for the reserve to open, and the adjust the AAD, and my eyes more importantly, to make the decision to go to the reserve at an altitude that will allow the slower reserve to work, just like high performance mains need to be opened higher. My partner argued with me about that idea lol.. This discussion will result in some “spirited” thoughts, and I think it is important that these thoughts are heard, as there are little bits of reality that can be extracted from any constructive view point regardless if it is pro or con to the subject. Who knows, even if we can make a test set up works as I want it to, it may end up just being used for our internal product testing because there is truly no interest in learning what happened.
-
The test standards are sure a mess aren’t they… Ok… Lets take a step back and get some perspective. To me personally the only performance specks that matter are those that directly relate to my survivability in a worse case situation. Basically, how many vertical feet does a reserve take to decelerate a jumper of X weight to a survivable descent rate from the time the pin is pulled, both at terminal and sub terminal activation speeds, and how hard it opens, as in, will it snap our necks. Do I assume correctly that is the only things that we as jumpers care about at terminal at 1000 ft? If that assumption is correct, then to hell with the bunch of confusing and vague standards… How about “we” as jumpers identify “our own” standards that we feel our equipment that we rely upon to save our selves with should be held to? I have always heard 300 vertical Ft and 3 seconds were the standards that had to be met. Has that changed? If we can agree on an acceptable vertical distance from pin pull to a safe vertical velocity, then we can test canopies and see how they perform in terms that matter to us. Distances from terminal are pretty much canopy dependent I bet, where as subterminal times and distances are very much pilot chute and rig reliant as the pervious poster pointed out. So there will need to be a couple different performance expectations, one for just the canopy and one for the system it is installed in, given that we only have one canopy, but can see both BASE type and Terminal deployment conditions. We also have to agree on a time from pin pull to the same safe vertical velocity as too fast of an opening will kill us just the same as impacting will. I am working on a test platform that will allow testing to be conducted vertically as apposed to horizontally as I understand if is “normally” done now, hence the arguments about how much distance was horizontal and how much was vertical yada yada… Is the idea of coming up with common sense standards that we want our gear to meet, and then testing gear in a controlled and documented manner, something that people are interested in participating in ?
-
I have seen so many different specks quoted from different TSO standards..... Simply, do reserve and container harnesses have the same min suspended weight and speed? I would imagine that reserve canopy would be timed from pin pull to reaching a target descent rate as well as distance? or does the clock stop as soon as the canopy unfolds, but is not generating any forward movement?
-
I made a small vac chamber once that had a cylinder with a piston attached to a scotch yoke that had a lever arm on it that was resting against a cam. I could pull a vacuum in the chamber and start a controlled descent. I could them cycle the cam and the piston would move causing a pressure ripple. I could also adjust the distance from the yoke shaft center to the cam to chance the ratio, which would increase or decrease the displacement of the piston as well as the speed. I made different cams to create different pressure signatures, just like you are thinking. I was based off of the G –Sleds at the GM proving Grounds. They used pneumatic cylinders much like the catapults on aircraft carriers. They could simulate a crash in reverse, by accelerating the test subject at the same rates as a crashing car decelerates. It is not a smooth curve, there are stages of deceleration as the crumple zones collapse. They have tapered and stepped pin that fits inside a very large orifice, and that controlled the cylinder fill rate. As the piston moved forward, the pin would move with it and depending on the taper and the steps, the test subject would accelerate in the same stages as the crash. I was trying to simulate certain conditions during a jump. It worked OK, but not as controllable as I would have liked. In order to have the piston functional, the vacuum chamber had to be very small, there was a definite piston displacement to chamber ratio in order to get the signatures to look right. The small chamber was very touchy to the bleed rate, and the venting controls I was using was not the best for the application. I have plans of building a larger chamber and have multiple pistons of different bores hooked up. Computer controlling would be a must, the previous design was all manual, and more for research than testing. Knowing what certain scenarios look like on a graph does allow us to do a lot of things. We use a simulation program that allows us to rerun previous drop data and see if the changes we made to the AAD software settings had a negative affect some where else. It also allows us to rerun extreme conditions that you just can’t recreate. Like when the rings got hung up on the rocket, you could not reproduce the failure, but if we have the data from a crazy drop, then we can rerun that exact drop over and over with different settings and then rerun as many other drops to check to see if it would have a problem, all without a plane. The hard part is getting the data, then it is fun to decipher what it is saying lol.. I was just looking at some of those radar speed guns that cops use. I had one years ago when I was racing, but it did not have a range indicator, only speed. I see that some of the new ones indicate distance to target up to 4000 ft. If you could record the distance and angle, the distance between the ground and the object could be determined, but the tolerance stack up might create to wide of a possible range? These things have laser sighting so I would think they would be reasonable, but there is only one way to know for sure. I want to create a test process that will allow AAD and reserve and reserve system performance to be tested to an extreme level of accuracy. Then take TSOed gear and see how it does. If there are canopies and containers that do not operate as they should, then I want to be able to identify them. Not to assign blame, not at all, but rater use that information to prevent caring on design ideas that in some instances come up short. And in the cases were everything is good, test it till it fails. I want the data that is generated to be good enough to stand in court if need be. This could be good and bad for a manufacturer I know…
-
I think of Airtec as a cartel lol… when you figure that they charge the US Military over $5,000 for a cypress, and other countries military just over $3,000 each, then I imagine this could quickly approach a $100,000,000 market for Airtec. They are pricing themselves out of the market, and with how they handled the latest recall has not helped any either. I am seeing more and more awards going to Vigil. Would the radar system that they used to determine the actual firing altitude be a practical method to measure reserve deployment distances and AAD testing? I am imagine a large and very expensive system, but I have no idea, if it is like the radar guns that the cops use then perhaps?.. From your experience I can see why Vigils have been used with the high altitude records, besides the connection to the rigs that were used as well lol… And I think you used a Vigil on the Armadillo Rockets right? I remember us talking about making an AAD for it, but it was too expensive at the time because we would have had to design a platform for it, as at the time the ADAPT platform is what we had on hand, and that is very big and bulky for the application. The new personal AAD platforms would have been perfect. The days of Government contracts = instant big money are over. Now, instead of money up front to build or study anything, it is payment on delivery, and if you do not deliver, then no money. This eliminates the companies that milked the system, always staying in prototype and never finishing anything, and it gives us little guys a chance because the big guys don’t want to mess with fixed price contracts that they have to float the cost of until complication and acceptance at the Government end. The problem for us little guys is funding availability. We are much smaller and leaner than the top heavy firms, so our costs are lower, but investors can be reluctant to fund a small firm, even with a Government contract in hand. I think a lot of companies lack personal with imagination, sure they are great engineers, but only as long as you stay inside the box. A piece of paper from a university an engineer dose not make, it is the natural talent that has been nurtured through effort and practice that makes an engineer IMOP. The ability to pull ideas out of thin air and then evaluate their potential is what has made this world what it is. Like the BASE rig project we were talking about recently. I had a crude method concept, but had not thought it through enough at an applicational level to know if the idea had any merit. You came up with a progressive series of design ideas, (as you were typing), that sound like they might actually work. The ability to perform always beats out paper IMOP. I can’t spell to save my life. I have always been amazed by comments that engineers have made about proposals for original concepts, and in some cases finished work that out preformed their requirements. I have gotten to the point to where I just sit back and say to my self, if out of all the information and ideas that are described in detail, all they can pick at is the spelling, then I am doing good lol… I always tell people, when I start building dictionaries, then there would be a problem lol..
-
Are you allowed to share what Airtec said regarding this situation? Also, to be fair, can you explain how the actual firing AGL altitude was determined? It would make sense to me that if the algorithm they are using does in some way dead recon based on velocity, then they would have created a firing altitude reference scale associated to the velocity so the actual activation altitude would adjust for the speed. For example, at a velocity of 100ft/sec then firing altitude setting would be 850ft to have the pack opening around 750ft. but if the velocity was say 200ft/sec then the firing altitude would be raised to say 975ft so the pack opening still takes place with in the 750ft area. It would be interesting to know how Airtec reacted to hearing about the performance you experienced.
-
300 ft/sec is just over 200 mph.. Any idea what the terminal speed for a no drogue tandem weighing = to the max rating? ( I'm not a Tandem instructor so I'm not sure what the limit is by the book) ___________________ John, I know you are an advocate for a shorter reserve bridal. Would the effects of two jumpers tight together (creating a larger burble), benefit more or less from a shorter reserve bridal? I think it was my second AAF jump I remember pulling the main and looking back at the spring loaded pilot chute trailing above the three of us. Then I did a better "check" and gave it enough air to pull the main bag out. Granted there should not be anyone around at reserve time, but in this case there was. Has anyone seen the video to have any idea how close the two were to each other when the AADs fired?
-
Would it make sense in regards to a testing standard for AADs that the AAD would have to function within the same parameters as a reserve is tested to, at least in regards to fall rate? The rationality is going beyond what the reserve is rated for in regards to fall rate is potentially disastrous, but then again the reserve has a loading variable. I can imagine a test process that takes a AAD and pushes it till it fails to operate properly, and if increasing the descent rate will push the actual activation altitude lower, then the users should know what the limit is so they do not exceed it without knowing what will happen. Swoopers know there is a speed limit to respect if they do not want 2 out on final, so the same should apply for activation altitude accuracy. If a jumper was going to be doing some high speed dives, they could raise the firing altitude setting to compensate for the higher descent rate, but then again, there is the limits of the reserve and survivability of a high speed opening to consider with that thought as well. We know the maximum “rated” limitations with the reserve and harness, but we have no idea what the limitations are for AADs. If speed is an issue then the manufacturers should put that in the owners manual what that speed limit is so we know to avoid descent rates above the limit, bellow a certain altitude so the AAD can catch up. Or if having two jumpers near each other causes a lower pressure altitude than a solo jumper, then close proximity should be avoided near activation altitude. (this is a no brainier to me, but some instructors can not help but to chase a student bellow the hard deck instead of deploying as a signal, “hay.. you might want to think about pulling now” but that is for another thread.) Am I over thinking things?
-
I have to apologize for the incorrect accelerometer axis (X should have said Y), in the above post regarding Lee’s question. It was 3AM when I posted it and after reading it to day I see some errors and it will not allow me to edit the post. So.. I am posting a corrective statement lol… I also see that I did not address Lee’s question about being able to correlate the readings of an accelerometer to changes in sensed pressure by the AAD where he asked it. The answer is yes but…, if the jumper were to fly in crisp movements like an aerobatic plan will snap role 90 degrees, then the correlation is pretty straight forward. If however the pilot does a lanuchivec (sorry on the spelling) , like a tumbling jumper, then you will see above 0 readings on all axis’s at the same time and with only one accelerometer keeping track of the movements will take a super computer I think. Having additional instruments to read independently so you have data to compare to makes identifying the combination of readings as a right turn or barrel role much easer. Using orientation to “tighten up” the firing “window” is very doable, but there will still be a “window” because of variables that are not considered in the logic. I wonder if they have to try to “predict” where the jumper is going to be in an effort to make up for the latency caused by high levels of averaging a slow sample rate? I am surprised that they would do it in such a way that there is a “fixed speed range” of the jumper is part of the equation, and going faster will through the formula off into the weeds or cause a loss in AAD “actual” altitude awareness so to speak. They are some vary smart people to have been able to get that to work IMOP.
-
Yes there are definitely issues with some rigs and packing practices, but the incident that this thread is really focused on, had two rigs, one a student rig, and one was an instructors, and both reserves failed to open. I can't imagine the law of averages would predict that both reserves would be stuck in the two different sized, and probably aged rigs. I think there was video of that jump from the instructor, and that would be helpful in determining their proximity and configuration at the time the AADs did fire. It they were on top of each other, then you have a tandem without a drogue, and the additional speed may have put the AADs behind the power curve. Or the burble from the two close together may have killed the reserve pilot chutes pulling the bags out. Or the burble through off the AADs sense of altitude… What ever happened it happened to both rigs. If they were both wearing identical team rigs then I could believe the tight reserve theory, but we are talking a student rig, (not saying that some one could have shoe horned a tandem reserve in there), and a instructor rig which I bet was in better shape and probably newer, ( but I an only guessing on that). It will be interesting to see the results of some recreations.
-
For the sake of discussion lets assume that a tumbling situation is rare, but in reality if there is any chance a scenario can happen, then you have to factor that in to the logic. Students are required to have AADs and all they do at first is tumble especially at the bottom end because they get REALLY stiff lol.. I would say a safe (general rule) number is between 125 to 200 Ft change in pressure altitude if you rolled over, definitely not any less but possibly more. It depends on a couple things, width of the jumper, speed, shape (arched or grabbing air etc.) The noise values are generally much lower than any “discernable” rotation. I say discernable because it is in the center of mass so you would need to rotate at a good rate during a center turn to get an X or Z axis reading. A gyro would be much better as it would pick up rotation of less than 1 degree pre second. As far as which way is down that is a different story. If you are falling stable, then no problem, you will get a X-Axis reading of about .9G because there is usually a little Z due to the angle of the rig, and that assumes a steady terminal fall rate. If you were to stand on your head then there would be a free fall moment, say about .4G for a moment then it would get back to 1G, minus any pitch which would be seen in the other axis. An accelerometer indicates orientation in a static state very nicely, but when it is in a dynamic environment, then you really need to know what is going on to have any chance of discerning which axis is down. With additional information from a Gyro you can tell what axis is rotating, and there for registering on the accelerometer’s complementary axis, so it can be factored in. The best instrument to determine orientation, independent of movement, is a magnetometer as it is not influenced my movement, only magnetic fields. Does that begin to answer your question? Or did I go off in a different direction? The basic answer is yes, what you are talking about can be done with an accelerometer, but it the values would be based on assumptions, like, it will not fall faster than XXX Ft/Sec, and if you go outside of those assumed parameters, then the logic will fail. IMOP, the best instrument for orientation measurement is a Magnetometer. What you are asking about regarding altitude calibration compensation for orientation, my AADs already can do. My AADs know if the jumper is in or has cleared the plane, or if they are being towed, or released from being towed, (in which case it will fire). I consider my AADs to be intelligent as they can determine the situation they are in, and make decisions based on those conditions. They will not fire in the aircraft at any altitude or descent rate. They will not get confused by going 500mph in free fall, or seeing below sea level pressures. All that has a price in that the processor is running at 100MHz and processing a lot of data, which is actually is handled by the data recorder. The other AAD manufacturers have nothing to worry about in regards to me stealing how they are doing it lol..
-
They could easily be processing the data from the baro sensor and have 7 checks, or conditions, so to speak that the processed data has to meet. It sounds like the Vigil and the Cypres are trying to Dead Recon position strictly using a baro sensor. Position (past and present) and Velocity (descent rate) are no brainers, and it sounds like they take those values and do more computations to possibly predict (in the case of Vigil) the jumpers location, or answer conditional statements. Simplistically complicated for sure. The problem with basing everything on one channel is if the base data, that all the calculations is based on, is wrong, then it’s a house of cards, and could explain why the Cypres 1 would lock up, not to say the Cypres 2 will not either, but if the base data results are whacked out, then the 4th and 5th level process results will be way out, I can see where it would say, hay, this is not right. The technology has certainly advanced since the Cypres 1, heck, I am using instruments that have gone through 4 evolutions in capability since I started using them. The instruments can do more, but that just creates more data that has to be handled. I am a simple guy and I do not like “complex algorithms”. Lol I would think that Airtec would promote that they are constantly updating the units and how the update improved the unit, but then again German philosophy would determine that as a failure to get it fight in the first place which is not acceptable. That is what I have taken away from working with a few German companies, it is not a quality driven mentality, it is a fear of failure that drives the sometimes overly complex and sometimes quality, that the marketing department promotes lol..
-
Data is a mess even at really high rates that are averaged down. As a body falls through the air there are frequencies generated to no end. And they are constantly changing as during the drop, so it is not as easy as filtering out a certain frequency range. Changes in frequencies indicate a change has taken place. Even just a change in amplitude means something changed to cause the frequency change. The trick is to look at the other instruments and see if they also picked up the change. Many times certain points on a graph of a given instrument are identified, but not were not solely identified by that instrument. After a while you start to be able to read the squiggly lines like another language. The trick is to let the data dictate the results, not what you want it to be or think it should be. If the clamed can be backed up, then it is, if not, then there are varying levels of confidence in the possibility, and ones credibility as a data interpreter is dependent on the validity of the interpretation as a whole... Thinking about it, the Cypres 1 design is over 20 years old, and the Cypres 2 is not to far behind it in reality. I would wager that the Cypres 2 code is largely based on the 20 year old code with some changes as they learned along the way, which is real life. The Vigil patent that I have that says something about an accelerometer is the same one that you have and after reading it again, I see that they say the use of an accelerometer is “cumbersome and expensive”.. Implying to me now that they are against using one, where as before I was scanning the doc and miss read the section.. Now I am even more nervous about being on a plane with any AAD lol… Vigil thinks an accelerometer with its additional 3 channels at 8 Hz is cumbersome, I am dealing with 10 channels at 20 Hz, storing them to memory, processing and evaluating, and executing if required. Lol
-
That is the first time I have seen the final report. We are supposed to meet with them at PIA and go over FFA’s report together. That was a very emotionally taxing project that will never really be finished. Every time we look at the hundreds of graphs that were made, we see more patterns that indicate things, and we think of new ways to analyze the data after we have had time to think about it. I hope that report is public information. If it is, you can see what the data looks like, and there is even some limited data from a Vigil. As for AADs and Accelerometers.. I just looked at the Cypres 1 patent and it mentions storing acceleration values but I think they are referring to values based on processing barometric data. I would have sworn that Airtec had an Accelerometer mentioned in the patent, but I don’t see it jumping out at me. The Vigil Patent does mention an accelerometer, and I have talked to the designer if the Argus and we talked about him using a Magnetometer as apposed to an accelerometer, so I may be all wet in regards to the Cypres. If the Cypers is only basing its decision on one channel of data, that is one complex algorithm.
-
One of the first things we plan on doing is trying to recreate that scenario as best we can with the data recorders in the reserve containers so we can get as realistic of an idea what those conditions are like. The Fact that 2 different reserves in different containers “seemed” to be deployed late and at the same time would indicate that the common link, the AAD, had some issues for what ever reason. This particular incident really is one to study for sure. Either the calibration was not right when they took off, or the conditions in free fall were such that they through the calibration off far enough to delay the indicated altitude reading?... I think it would be good for the AAD manufacturers to release the data from the AADs involved in an incident to show that it worked properly, even if in reality it may not have, as, if the “zero” was off then the data would look normal except for a shorter time from activation to impact. If the indicated altitude was skewed due to the two of them in close proximity, (nothing we do not do every jump, granted generally not that low), then I would expect to see the baro graph indicate high rates of change prior to activation and right after, and again with a shorter time from activation to impact. Most of the data I have is owned by the Gov, so I am very anxious to get the free fall AAD beta unit done so we can start collecting some comparative data. Is this kind of information of any interest to the jumping public or just a few of us?
-
Last year there was a BLM fatality during a series of test jumps, for what I am not allowed to say, but they were using my Parachute Flight Data Recorder on each jumper and the free fall data of the fatal jump was collected. There was video from the plane and the ground, but where everything went wrong neither had any useful footage. To my knowledge, this is the first time that there was an incident with a "Black Box" to collect data. We were contracted by the Government to analyse the data of the incident as well as the other jumps to try to provide the investigation team more detail as to how that particular jump compared to the others, and what the jumper was experiencing out of sight of the cameras. This was enough of a challenge due to the how their equipment positioned the jumper in free fall, but we found out that the data recorders were not mounted properly in any respect. We were able do some hanging harness tests and found new calibration reference for the incorrect orientation so we were able to get a more realistic idea of the jumpers orientation during the jump which was of great interest by the investigation team. This particular data recorder was designed to measure parachute flight performance, not a free falling body, as such, the instrumentation was not perfectly suited for collecting this type of data. The data recorders had a 3-Axis Accelerometer, Z-Axis Gyro, Baro pressure, Temp, Humidity, digital compass, and air speed (not used during the jumps in question). It was quite a challenge, as of all the data we had from many different conventional drop tests really did not help us other than identifying the exit and canopy deployment. We used these points and went in both directions. We were able to come to a conclusion as to what happened, up there, but obviously not exactly why it happened. I was actually surprised to see how much detail we were able to see in the data once we knew what we were looking at. I can't talk about the details, but after doing that I can definitely see the value of a free fall data recorder on every service jumper. I have added a 3-Axis Gyro and a 3-Axis magnetometer (configured different than a compass), and my Military AADs have these free fall data recorders built in and record every aspect of a jump. From what I understand every AAD has an Accelerometer except for the Argus which used a Magnetometer. Although useing a single 3-Axis Accelerometer to identify orenation is easy to do in a static state, it is a whole different matter when the object is rotating on more than one axis or there is straight line energy being input. As I am sure you know this is getting into the 6 or 9 degrees of freedom arena, which requires a good amount of live processing power to utilize at 200 ft/sec. No Barometrically referenced AAD will fire at constant altitude regardless orientation to the pressure front (relative wind). There will be a "window" in which the AAD will fire depending on the orientation of the jumper. Now as far as the AAD is concerned, it "usualy" has a set of fixed firing altitude, but if it is in the burble it will fire at one AGL and if it is exposed to the pressure front it will fire higher, if it sees an average, then it will fire in the middle (+-). Adding some intelligence to the processing logic along with some additional sensors besides a baro sensor, allows the AAD to tighten up on the firing tolerance quite a bit as well as reducing or avoiding firing when it is really not called for. But that requires lots of processor involvement and memory, which reduces battery life or requires larger batteries. From what I can remember, and they may have changed this since then, but I recall that the Cypres can get confused if it sees conditions that are outside its limits and will shut down. I recall some of them shutting down on a helicopter ride at the WFFC? If it still is unable to handle certain situations then it is certainly possible that the logic could have issues when encroaching this limit? Even if it shuts down, I find it hard to believe that the error was not logged internally and the data up to the point where it shut down would not be there. I have seen quite a few "suicides" of Cypres owners that "could" be due to it shutting down. I am not sure what Vigil or M2 does, or if they even can "get confused". If the Cypres code is such that it can get locked up, or confused by rapidly changing conditions, that would imply that it is trying to draw conclusions based on previous data and when the new data doesn't match what it expects to see, then the logic tree may hit a dead end, no pun intended..
-
It does seem like the thinking, "no body, no crime", doesn't it. As, if there is not any information the container type and age, reserve make, age, and maintenance, if there was an AAD or not, and if so, the make, age, and maintenance history, let alone any data that they "may" have in memory, then all will be good in time... In time 90% just forget about the fact that someones reserve did not open in time (assuming it was activated at an appropriate altitude) but again, with videos of reserve pilot chutes in tow, it is hard to argue that the system was operating with in TSO standards. I by no means mean to imply or create the idea that the manufacturers are knowingly producing gear that will not work as they advertise. I too have had the opportunity to get to know some of the founding fathers so to speak and I know that they are deeply troubled when there is an incident. The truth is nothing to fear as it is the cover up that is always worse. I think is looks very shady to a woofo that we do not have detailed incident reports available, like "we" are attempting to hide a bad safety record or something. If a piece of equipment did indeed fail to operate properly, which happens ever day in real life, (just look at the most recent air bag recall), then that information needs to be studied and changes made. Now granted that if there are several similar incidents that involved the same equipment, then there is a marketing problem for those manufacturers. There are recalls on our gear all the time, the idea of hiding the details of an incident is just silly IMOP.
-
The options for relatively high speed digital absolute pressure sensors has been very limited until a few years ago. The reason I was still using Analog pressure transducers was because the digital ones had such a slow refresh rate. Today there are a couple of different digital (MEMS) sensors with refresh rates available over 100 sps, but there is usually a trade off with the resolution as is the norm with many other digital instruments. If you are looking for one PM me and I will send you the part numbers to a one that I have used and the one that I am currently using, the only difference is features like on-board processing, alert thresholds etc.. It scares me when I see some of the pack jobs that some riggers do, and the gear owner dose not question it because the rigger is their friend or the cool guy on the DZ.. The reserve is our last ditch chance to save ourselves, and it's maintenance has nothing to do with a popularity contest lol... The more data that is out there the better!!
-
Is there any reason why those reports are not available to jumpers????
-
I was thinking about what you said and I would say you are correct in that the actual firing algorithm for any AAD is crude, in that it is a altitude and descent rate function. The magic is in how the raw data is processed. There are lots of different ways to get an AAD to fire with in a window of altitude at with in a range of speed. Perhaps there is a language barrier issue when trying to describe how the Vigil works? Personally I agree with not making any logic or algorithms public because they can not help but evolve over time. I protect my logic as a Trade Secret. Hopefully the latest Vigil update will lessen the hair trigger tendency they seem to have and from what the memos you have sighted seem to back up. Perhaps they are that way because of the delayed data due to averaging that you also pointed out as being possible from how they describe how it works? Really, if you think about it, from the time that the processor authorizes the and executes the firing, to the time the pyro agent is ignited should take no longer than 20ms, which at 200 ft/s that still covers some distance.
-
Batteries and Capasators Aside of the time required to charge a super capacitor, once the firing circuit is triggered, the power will reach the cutter as fast as an electron moves. Once power reaches the cutter initiator the standard max activation time is 10ms. I have had a custom cutter initiator designed for my cutters and they have dual ignition bridge wires for redundancy, over kill I know, but it the engineer thought it would be easy to do given the design, so we went with it. Anyway… A capacitors ability to maintain a voltage level at a given discharge rate depends on the capacity of the capacitor. One of my cargo AADs has 8 individual firing circuits and there are several capacitors in parallel to be able to maintain voltage and currant levels with all 8 circuits fired. Yes it takes time to charge a capacitor, but as long as that time is factored in then it is a non issue. Of course, exceeding the descent rate that the charge time is factored for will result in a “late” activation. When deciding if one wants to / can, fire a cutter directly from a battery, one needs to look at the worse case scenario, an old battery with only ¼ charge left that is cold soaked to the min temperature speck. In this case it takes a pretty stout battery to be able to put out power on demand with out collapsing. There are two common designs for hi-density batteries, Spiral and Bobbin core construction. Bobbin core are designed for long term low currant draw applications, and Spiral core are for high amp output and pulse applications. AADs have a requirement for both technologies so, in the case of Vigil they have both types of batteries, one to power the processor, and one for the high demand of the cutter. Another way to manage the different power demands is to slowly charge a high output capacitor just before it is needed. I looked at a capacitor firing circuit and given the nature of the application (exits as low as 500 ft AGL), it would have had to charge every time the AAD was turned on so it was ready to go given the little time there is at that altitude. That would waste a lot of battery power, so I went with a dual battery design, but different than what Vigil has. Sample rates and filtering You are correct that the more you average the later the response is. 6 to 8 sps seems to be the range for the AADs on the market, looking at maybe 4 channels? The data recorders in mine are recording 10 channels at 20 sps in contrast, but the AAD is still a traditional AAD that is barometrically referenced, so really inside the box is two separate devices, a data recorder and an AAD. You mentioned some in aircraft firing instances, which every electronic AAD has done except for the M2 given it is new and is just starting to get some seat time so to speak. Personally I do not think that it is acceptable for a processor driven AAD to fire at it’s command while in an aircraft, regardless of the aircraft location or descent rate. I have spent several years working on an “intelligent” design for Military cargo and personal applications that is situational aware and knows if it has “cleared” the aircraft. I say “cleared” because one of the malfunctions is a static line jumper in tow, in that instance, an AAD fire can be disastrous, as any in aircraft activation has the potential to be. This intelligence is handled by the data recorder and requires a lot of processing power which requires more battery currant and capacity compared to the traditional electronic AADs on the market. I certainly can not claim a battery will last 15 years or 5000 jumps lol. But I can and do claim that it will not fire in an aircraft period,… well if a wing were to brake off, then maybe… one of the tests we are going to do next summer is put one of every AAD next to mine, in an aerobatic plane, and see if the pilot can get them to fire. In the lack of intelligence, the logic and settings have to be very tight as was mentioned, and that tightness is dependent on the consistency of the instrumentation out put quality and accuracy, as well as the speed of the sample rate. Also battery life is dependent on the processing demands and the civilian market seems to be demanding extreme battery life for the power requirements that this type of application “would” demand given more intelligence was programmed into the AAD. Thoughts so far.. This has been a great experience. The ability to discuss possible technical issues, albeit hypothetical as we do not have, and will never see the data that would allow us to prove or disprove any theories, is great, and rare from my experience with all types of forums, props to everyone! I definitely like the idea of displaying the zero calibration changes throughout the day so the jumper knows what their equipment is doing, none of us would board a plane without zeroing our altimeter, so why would we not do so with our AADs? I also think a log book of the AAD from the initial test results at the time of validation, every maintenance test result, part replacement and why, till it has reached its end of life should be a requirement. As my partner pointed out, that is required for a reserve, so why not the device that “might” activate it? I think the Military will like that. This summer I will have the Free Fall AAD ready for testing and will start using the built in data recorder to measure burble affects on the indicated altitude as bodies close in on each other, like an AFF jump would be. I will publish all the data that I collect so we all can have a better understanding of what is going on in that little black box. From there I will start to add sensor input from the container, such as pin extraction detection, pilot chute acceleration, bridle pull force, free bag acceleration, time from cutter fire to pilot chute acceleration, etc.. Once we develop a method to measure the performance of a complete “off the shelf” rig, then the next time there is an incident, there is no excuse not to be able to test that combination, should it be in question, remember that 99% of the time it is jumper error that is responsible, but when you see a video of a reserve pilot chute in tow, or have two separate jumpers impact with their reserves at line stretch (at the same time)then that equipment, including the AADs, should be instrumented up.