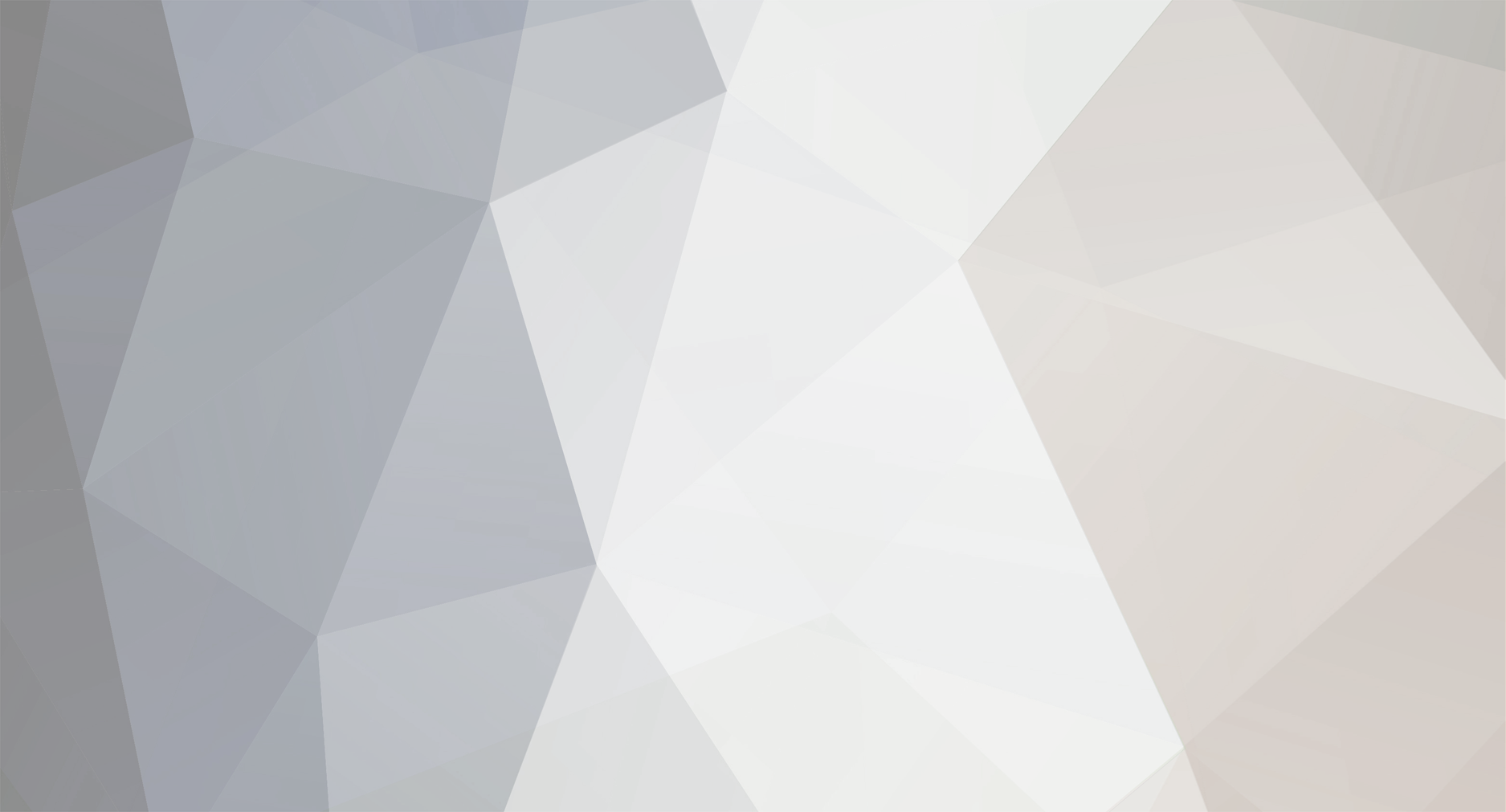
DBTECH
Members-
Content
232 -
Joined
-
Last visited
Never -
Feedback
0%
Content Type
Profiles
Forums
Calendar
Dropzones
Gear
Articles
Fatalities
Stolen
Indoor
Help
Downloads
Gallery
Blogs
Store
Videos
Classifieds
Everything posted by DBTECH
-
Seems that no one here has mentioned the most important factor in preventing line dump, and that is, large line bites. I don't object to Silicone on bands, but I do object to line bites smaller than 2.5 inches for locking, and 3 inches for post locking. (preferably 3.5") There is a HUGE difference in line dump potential between a 2 & 3 inch line bite, because of the "mass/lever effect" outside of the stow band. BTW guys,--this topic/thread, belongs be in- "Gear and Rigging" Dave Brownell Mesa, AZ
-
For your reference-- This same 21" ZP PC was used on a Spectre 170 for 295 jumps with no problem, before it was put on my Cobalt 135. Dave Brownell
-
An excerpt from my "yet to be published" article, entitled-- Fast openings/Slow openings--The Real Physics of slider rebound; plus invention revealed. (Patent Pending) By David B. Brownell An excerpt from that article-- Another way to reduce snatch force energy and the evils resulting from it, is to go with a smaller pilot chute. A smaller pilot chute will result in the bagged canopy reaching a slower speed relative to the jumper at last line stow release* This slower speed will result in lower slider stop line rebound energy. A smaller pilot chute will also lessen the chance of line dump. How much smaller do you ask? Well now; I'm jumping an Atair Cobalt 135 with a 21" zero porosity (ZP) pilot chute that I made. I'm sure that this scares many of you, but please listen to my logic here. Back a few years ago we were jumping canopies that weighed eight to twelve pounds. Many of the pilot chutes used then were 30" to 32" made of F-111 fabric. If we were to go with a canopy of half the weight, say five to six pounds, "logic" should tell us that we would need a pilot chute of half the area with approximately half the drag; which, in my mind, is true. For those of you that are thinking a square function, that only applies to airspeed changes, not area changes. A 21" pilot chute has half the area and approximately half the drag of a 30" pilot chute. Also, don't forget that we are talking here about an F-111 pilot chute that degrades with use. A ZP pilot chute would not degrade. Based on the above factors and testing I have done in the field, I believe that we can go with pilot chutes made with ZP fabric under 21" for canopies under six pounds. Dave Brownell
-
I don't consider myself a big fan of the X-Files, but if it happens to be on, I will "monitor" it. As far as my stand on the universe--the universe had no beginning, therefore, it could not have an end. There's no question in my mind that intelligent life is very common throughout the universe. What I believe, not to be "very common" is their capability for interstellar travel in a "reasonable" time frame. (reasonable is, of course, relative--(like my article at--> http://www.dzsports.net/news4.html Dave Brownell Mesa, AZ
-
The original FXC model 12,000 was not designed by FXC, as FXC bought out the company that designed it. I believe the company was called "High Tech Corp." As far as the Astra, I can't imagine anyone in that company (FXC) that would have the electronics/mechanical education to design such a unit, which leads me believe that the design of this unit was done by another company, and is also being built again by another company for FXC. Until proven otherwise, this is what I believe. Can the same be said about a Cypres? Skies, Dave Brownell DB Tech
-
At terminal V, not having the steering lines routed through the rear slider grommets, in my mind, would probably guarantee a very fast/hard, gut wrenching opening. The chance of a "steering line over" would probably increase. Dave Brownell
-
I will agree with your "highly loaded scenario," as the "ratio" of induced drag to parasitic drag is much higher, as apposed to lower airspeeds with much less parasitic drag with similar or higher induced drag. Let's face it, the drag on a 28" PC could easily be 30 lbs at 60 MPH. A non collapsed slider on the other hand--hard call?? BTW: The parasitic drag of your body under canopy at 60 MPH forward speed is about 25% of your body weight! BTW-again--not negative vibes, but I'm always in this mode-- "Always Question the Validity of the Obvious" Skies, Dave Brownell DB Tech
-
Justin said It might be a "placebo effect". I don't know or care, as long as it stops the stupid flapping noise behind my head. I'll second that big time, with two thumbs up ^^
-
Jtval said-- I collapsed my slider this weekend. it was cool. not much of a change (i am on a big,low loaded main) but enough to know that there was a change in flight. DB> Sounds like a classic case of the "placebo effect" in action. Dave Brownell
-
My last post read-- The long term durability of Slinks has yet to be shown/proven. I would like to see pull test numbers before and after 1000 jumps. (both pull tests to be done with same size dia pins) Dave Brownell Spectre230 said-- I think the people that make these links should set a service life for them. I'm sure they don't last forever. You also need to put a mark with fingernail polish on the link so you can tell when they start to loosen up. Check them after every jump or make sure your packer does. DB-- As you can see, I was referring to Slinks here, not Mallion Rapide links, which I consider to have no service time limit in this application. As far as your comment about the nut on Rapide links needing to be checked on every jump; I totality disagree with this need, as the nut will not loosen up if properly torqued. If your so concerned with this, then use tight silicone slider bumpers that will prevent the nut from turning, or use Loctite. Dave Brownell Mesa, AZ Edited by dbtech on 6/9/01 02:27 PM.
-
Hello Monk (Spencer) Please send me your E-mail address, as I have a letter for you. Dave Brownell Mesa, AZ dbtek@juno.com
-
The long term durability of Slinks has yet to be shown/proven. I would like to see pull test numbers before and after 1000 jumps. (both pull tests to be done with same size dia pins) Dave Brownell
-
Excerpt from an earlier post-- I would agree that Slinks would probably fail at a higher number than 3.5 Maillon Rapide links, (mini links) but not likely higher than #4's, and definitely not higher than #5's. Dave Brownell
-
When reading the title of your topic/thread, I assumed that you meant that the link deformed, with the nut properly torqued, because of a gut-wrenching hard opening. Yes, this has happened before! As far as Rapide link nut tightening/torque is concerned, yes a quarter turn after max finger tightness/torque, is a "nominal" rule of thumb. I, myself use a torque value/level that is based on my mechanical background/experience. I am not an advocate of the use of Loctite in this application, as I feel that "proper torque" will assure nut retention, but to each their own. Yes, tight silicone bumpers will act as a "back up." For your record, here is an excerpt from an earlier topic/thread regarding Mallion Rapide links. db My new Cobalt 135 came with #4's, which I consider to be the "ideal" Maillon Rapide link. As far as 3.5 mini's are concerned, I've always felt that they are pushing the envelope to much, with very little strength margin as compared to #4's. Keep in mind that #5's were the norm before 3.5's.(mini's) 3.5's (mini's) are one half the strength of #5's! Number 4's fall in the lower middle between 3.5's and 5's. Note: A #8 Brass or 25mm stainless slider grommet will go over #4's with no problem. Dave Brownell Mesa, AZ
-
Alan said-- So far on my 89 VX at 2.4+ it has been about 6mph slower with the slider un stowed based on radar gun readings during my landing approach. That is nearly 10% slower. DB> I could maybe buy into a number "approaching" an 8% loss in airspeed with a VX with the slider not collapsed/stowed, but radar gun readings are not IAS or true airspeed, but are in fact ground based readings subject to errors brought about from wind/wind shear conditions, which are different on every jump. Let's see numbers with an actual "air speed indicator" that has good "confirmed resolution" in one MPH increments. Model/conditions--- Toggles up--stabilized flight-- slider not collapsed, then with slider collapsed/stowed. (comparisons done with no change in the body shape/position--drag coefficient of the jumper) Dave Brownell
-
Alan said> >The change in airspeed on most recreational canopies MAY ONLY BE 2-3 mph or less,--- DB> As asked before--"Show me the "MEASURED DIFFERENCE" in forward airspeed with the slider left alone, vrs it being totality collapsed/stowed." "Beware of the "PLACEBO EFFECT" in all claims of better performance." Dave Brownell
-
The reduction in parasitic drag with a collapsed/stowed slider is a very-very small percentage of the total drag, both parasitic and inducted. Show me the "measured difference" in forward airspeed with the slider left alone, vrs it being totality collapsed/stowed. Dave Brownell
-
Less believable---E Bola virus! More believable---Meningitis db
-
If designed/constructed properly, I prefer a Cordura/Parapack BOC pouch because of the durability factor. I own a Reflex with a Cordura pouch. Dave Brownell
-
Go to--> http://www.extremefly.com/dealers.htm Edited by dbtech on 5/30/01 10:23 PM.
-
With the rings assembled properly there is about a 25 to 1 "ring" mechanical advantage. (not considering the loop mechanical advantage of a nominal 2 X 25=50) If the small riser ring is passed through the harness ring, then the ring mechanical advantage is less than five, or less than ten at the release cable, as apposed to fifty with the rings assembled properly. Dave Brownell
-
Before I moved to Arizona, as pilot I put out about 5000 static line students at Hinckley, Illinois. None died, but of course there where some broken bones landing under cheapos and T-10's. On a load that I did not fly, a 350 pound first jump student broke both tibias landing under a 44 foot cargo chute! All of the static line jumps at Hinckley were direct bag deployment. (no pilot chute--bag stays with aircraft) Dave Brownell
-
For the record, I thought some of you may have interest in this question asked on rec.skydiving. db Jaime asks: >>Can anyone tell me anything about integrity risers? >>Thanks for your time. Integrity risers were first dreamed up because of the fear of riser failure only on the side with an RSL connection, during a very fast/hard opening, which would result in a main-reserve entanglement. (Yes, it has happened. Integrity risers are built without a grommet in the riser for the cable loop. Instead, there is a tab on the ring side of the riser that has the grommet. Integrity risers are installed on the harness ring in reverse (riser rings toward rig). Integrity risers are stronger because of their absence of a grommet hole. There are two negatives regarding integrity risers. The first is the fact that the loop mechanical advantage is close to half that of conventional risers, which in fact reduces the total mechanical advantage to close to half also. The reason that they have reduced mechanical advantage is because there is no longer a loop around the small ring, but a near straight line between the loop attachment point and the locking cable. There is in fact recorded cases, where under a high G spinning malfunction, where the release cable was pulled into the grommet somewhat, due to the higher forces, which resulted in a very hard release cable pull. When you consider this factor combined with the high friction of soft housings, you can see the potential of a deadly combination. This is not just my opinion, but is one shared by many in the industry. As far as stainless housings, I recommend keeping them clean, along with clean cables with a little silicone applied. Regular maintenance will keep them at a low coefficient of friction. The second negative is the possibility of not getting a riser release because of a combination of lower harness rings locations and a somewhat face to earth under a low drag malfunction. Rigs/harnesses made today are made with this in mind to assure high harness rings locations. I do not use an RSL, but I do like the strength advantage of a hole-less TY-17 riser. As far as a canopy with high spin rates associated with malfunctions being used with integrity risers, I myself have no problem with integrity risers, because of the factor of housing/cable maintenance. I once had a very fast/hard, brutal opening on my Spectre 170 with integrity risers. When I examined the loop/grommet/cable point there was no evidence of penetration of the cable into the grommet, which in my opinion, gave me a better "feel" for the total mechanical system. I recommend the use of the short metal excess cable housings installed in the stow channel in all risers, be it type 8 or type 17. These housings will prevent release cable capture/binding after a severe riser twist due to a severe canopy spin. 1/4" OD X 0.035" wall Teflon tubing works great also. One tack with Nylon wax cord 1/4"-3/8" from the inserted end holds it in place. I'm not trying to put down type17 integrity risers, as I have used them myself. Ultra blue skies, Dave Brownell DB Technologies Mesa, AZ
-
Craig said: Seriously though, I am GUESSING about 12in released riser travel as the second riser is being released. I noticed the differences in the cable lengths (from loop to end of cable) when I was inspecting my release system a few months back and chalked it up to design and wanting the RSL side to release first to possibly reduce the risk of reserve PC entanglement. Another consideration besides wanting the RSL riser to release first would be housing flex/stretch due to a loaded harness. This might or might not be equal depending on the mal (more weight suspended under the RSL side would stretch the harness/housings more on that side which would use some of the cable length as a result. FWIW my RSL side release cable is 1 1/4" longer than the other side. Craig DB> You do mean the "non" RSL side, ideally releasing first. I would agree with 12" - 36" being a riser release difference figure. Dave Brownell
-
I believe his name is Ralph in California. (maybe near Paris?) db